Cleaning quality controls
Cleaning and accredited checks, detailed reports, action plans, data collection in the field and cross-analysis
Contact usForts de notre expérience, nous avons développé une expertise dans le nettoyage et nous vous assistons pour auditer la qualité des prestations de votre fournisseur de services.
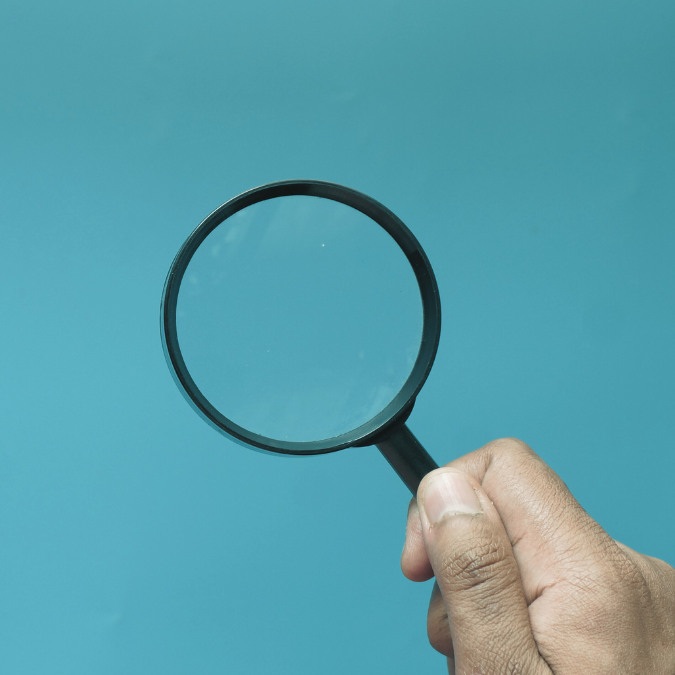
At any time during your contract, we can carry out external inspections and audits to measure the quality of our services.
Importance of cleaning quality controls
Carrying out
cleaning quality control is essential to maintain
high standards of hygiene and cleanliness.
These quality controls make it possible to accurately assess whether the services provided comply with the requirements set out in the contract, by quickly detecting any gaps or risk areas. They provide a clear picture of how the service is performing and any possible improvements.
By identifying problems as soon as they arise, quality controls help to ensure cleaning processes and methods are adjusted proactively.
The inspection reports provide valuable data to help to help implement appropriate improvement plans (staff training, process changes, etc.).
The FLASH 2.0 inspection module
The FLASH 2.0 inspection module in the QUALIPSO Suite is an innovative digital tool we've designed to guarantee precise and rigorous monitoring of the quality of cleaning services.
The FLASH 2.0 module enables you to carry out objective quality controls, based on precise criteria, in accordance with EN 13549, a standard renowned for its stringent and rigorous demands in assessing cleanliness in the cleaning industry.
FLASH 2.0 can be used on a smartphone or tablet (iOS or Android) via the IPSO Mobile app. This means checks can be carried out on the ground in real time, which makes it possible for users to
collect reliable data that can be instantly synchronised
for optimum monitoring of services.
Whether it's a one-off or a recurring inspection, FLASH 2.0 provides you with accurate, objective monitoring that aligns perfectly with the requirements of your contract.
The requirements of the EN 13549 standard
Our inspections comply with the EN 13549 standard in every respect.
An inspection is a snapshot of a situation at a given time.
Its purpose
is to take on objective view of an impression that is generally subjective.
The customer will pay for 100% quality. A margin of up to 15% non-quality is accepted. An inspection must therefore reach a minimum of 85% on average.
The minimum Acceptance Quality Limit (AQL) will depend on the category of premises. For example, the AQL is set at 90% for smart working or sanitary facilities, 85% for a traditional office or kitchenette, 80% for a secondary corridor and 75% for a technical area or car park.
The AQL can be adapted to suit your needs.
Le
contrôleur procède toujours de la même manière dans tous les types de locaux et vérifie au moins un exemplaire de chaque type d'objet dans un local
(fictif). Il en contrôle 25 % s'il y en a plusieurs.
Pour chaque objet contrôlé, il note les manquements constatés : poussières, taches, tartre, etc.
The weighting of faults depends on the type of item inspected (floor, task or furniture) and the number of items to be inspected at each site.
The inspector will not note any non-conformities that have occurred since the last cleaning operation. For example, they will not take into account any crumbs on a kitchenette table at 11:00 am.
Sampling on premises
To ensure that the results are statistically representative, quality control is based on sampling your premises in accordance with the ISO 2859 standard.
ISO 2859 prescribes the sampling procedures for inspections by attribute indexed by acceptance quality limit (AQL) for lot-by-lot inspection.
The ISO 2859 standard proposes three types of sampling: in-depth, normal and light.
QUALIPSO has developed its own sampling curve (blue curve on the attached diagram). This curve is more demanding than the in-depth sampling curve for small buildings and is similar to the light sampling curve for large buildings.
Ultimately, an inspection covers a predefined number of sites per AQL.
Standard, standardised or accredited inspections
There are three types of inspection:
- Accredited : these
strictly comply with the ISO 2859 standard in terms of sampling AND are accompanied by a "contract review" signed by the customer, that is
tailored to each change.
These are the only inspections that carry the BELAC logo. They are therefore automatically recognised by the social partners. - Standardised: these
comply with the ISO 2859 standard in terms of sampling, but are not accompanied by a contract
review.
- Standard: these are inspections for which sampling is not possible because we do not have access to the structural data (metrics).
After completing an inspection in the field, the inspector will synchronise it with QUALIPSO Suite. Once back in the office, they can then add a comment and validate it.
The inspection will then be sent automatically to everyone due to receive it.
The inspection reports generated by the FLASH 2.0 application provide a detailed, in-depth overview of cleaning quality.
They are made up of the following sections:
- the overall result: compliant or non-compliant
- results by AQL
- changes in the overall result for this building, month by month
- results by category of premises
- a detailed list of the premises inspected and the points calculated, based on the shortcomings observed.
- an analysis of any shortcomings
- the inspector's comments
- photos taken to illustrate the main shortcomings
In addition, a whole range of analysis reports can be generated, depending on the customer's needs, for example:
- a general dashboard
- a report presenting the monthly results for all buildings
- a report analysing faults by item/inventory ‒ either a comprehensive report or for a specific category of premises.
This enables corrective action plans to be drawn up, which will have an immediate impact on the quality of the cleaning. - etc.